A Magnetostrictive Sensor is a Part of a Continuous Level Measuring System Consisting of a N
Level Switches
Introduction
This article takes an in depth look at level switches and their use.
You will learn more about topics such as:
- What is a Level Switch
- Uses for Level Switches
- Types of Level Switches
- How Level Switches Work
- And much more …
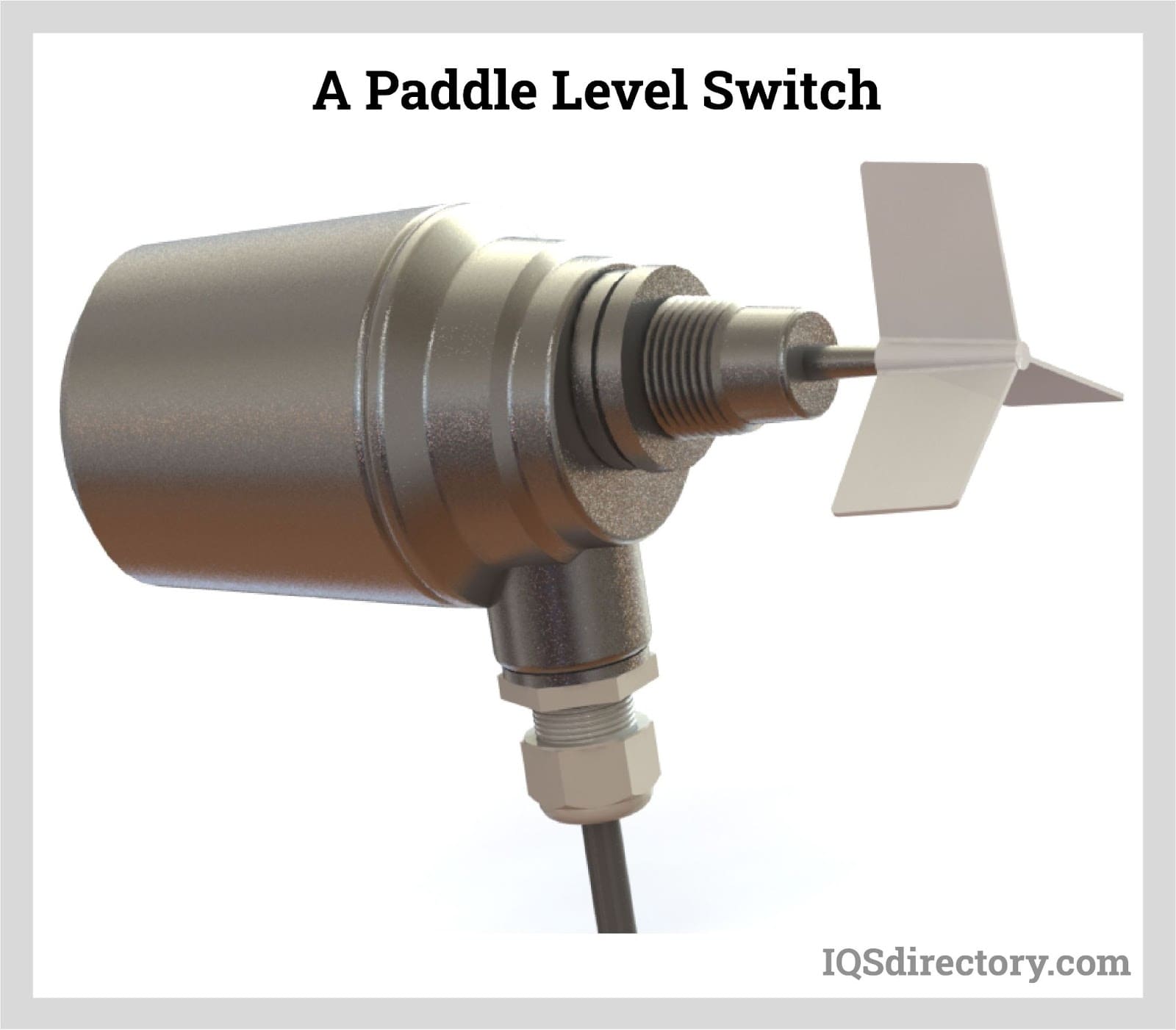
Chapter One – What is a Level Switch?
A level switch is an electrical or mechanical method for measuring the level of a liquid, powder, or granule material. It is designed to activate an alarm if the material level in a container passes a predetermined height or depth. When a level switch detects that a tank is full, it is referred to as full or upper limit detection. If the level of the material drops, indicating that the tank is nearly empty, the switch will also provide an alert, which is referred to as empty or low level detection.
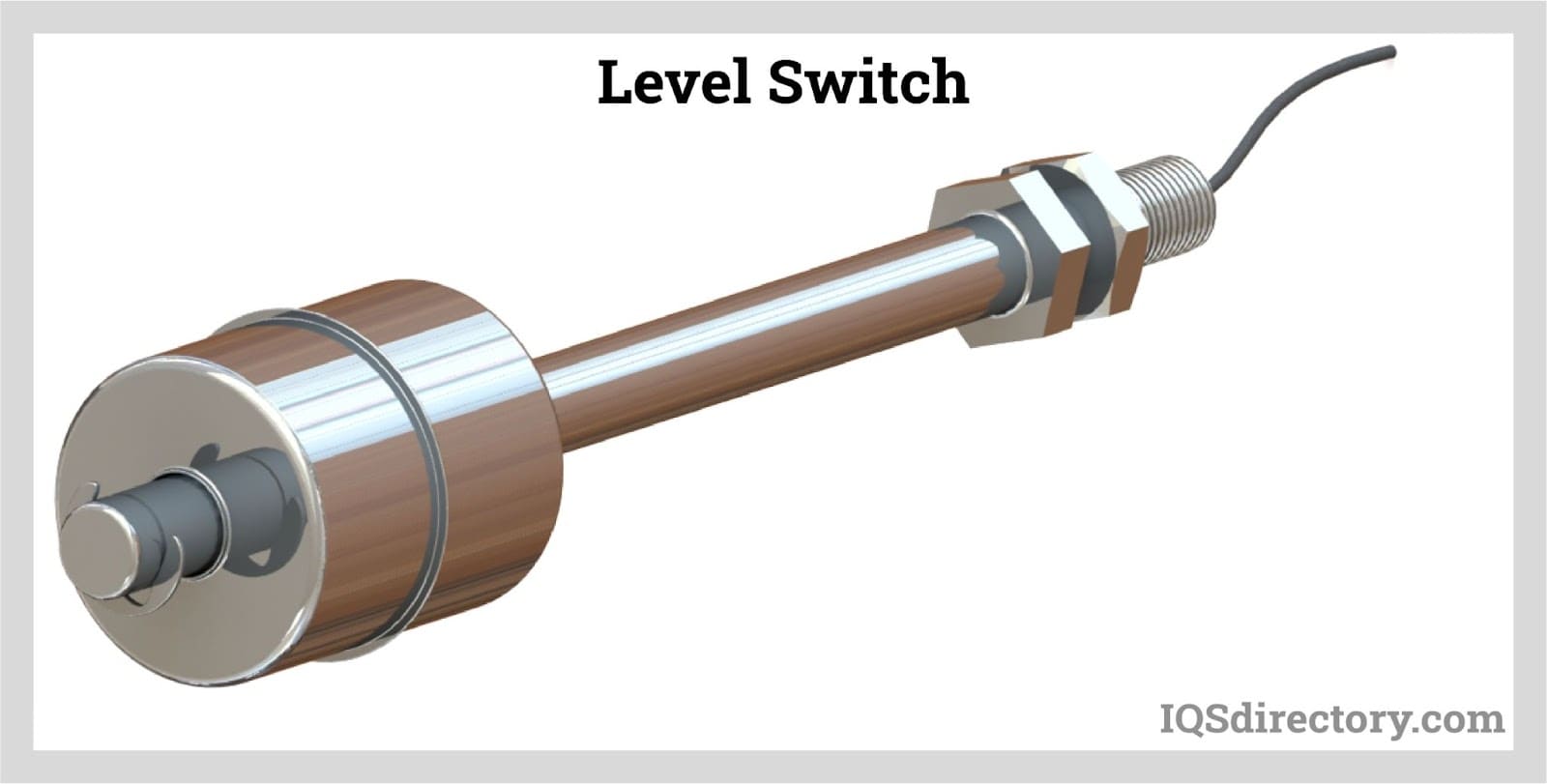
Level switches are an essential part of production operations and are used in harsh conditions where there are extremes in temperature, pressure, and vibrations. The diversity of level switches makes them applicable to any conditions for measuring a wide array of products. Their accuracy, reliability, and durability are a necessity for the efficiency of industrial applications.
Chapter Two – Types of Level Switches
There is a type of level switch to fit any type of product or application. They are used as a measurement device, a monitoring control, or warning alarm, such as when to turn a mechanism on or off. Level switches are equipped with a mechanical or electrical output, depending on their design, and can be open or closed.
Of the many kinds of level switches, the most commonly used are inductive, thermal, float, rotating paddle, and ultrasonic, which are used in tanks, silos, and different types of storage bins. For fluid level control, level switches are placed in control valves or pumps to help maintain tank levels and prevent overflow.
Level switches fall into two categories, which are point and continuous. Point level switches include optical, horizontal float, vertical, and ultrasonic. Continuous level switches include submersible, ultrasonic, and capacitive. The type of level switch used is determined by the types of measurements and the environmental conditions.
Level Switch Types
Capacitive Level Switch
Capacitive level switches are designed to measure corrosive liquids, high temperatures, and liquid levels in sealed containers. A capacitive level switch works on the principle of capacitance. It has an electrode that changes when the height of the medium changes and causes its capacitance, the ratio of its electrical charge, to change. The sensing mechanism changes the level or height of the medium into a current signal transmitted to a secondary instrument or computer.
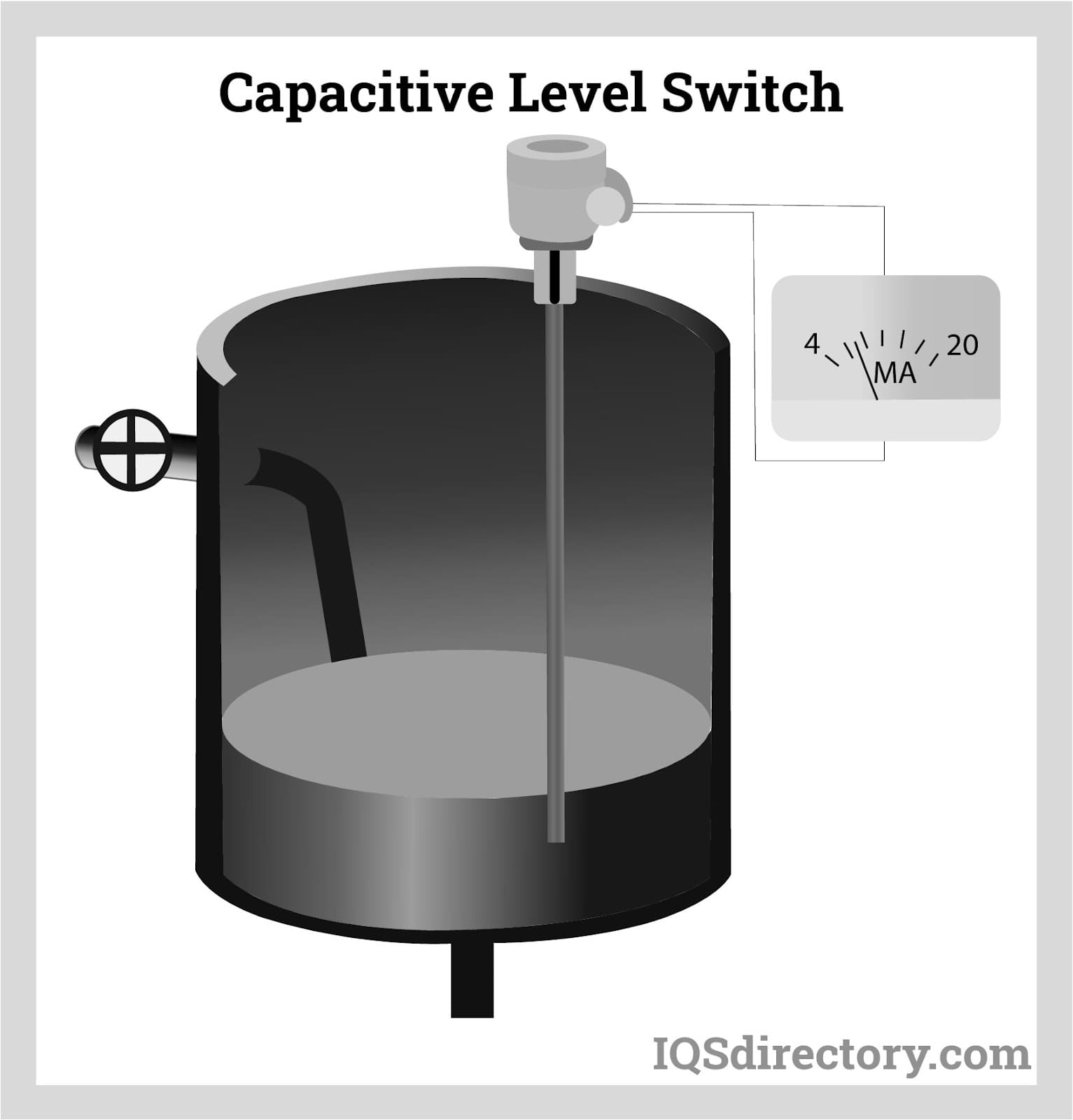
Conductivity Level Switches
Conductivity level switches have sophisticated and highly sensitive sensors that record slight changes in the level of a liquid. They have conductive probes that are completely insulated electrodes except for their tips to avoid electrical bridging. The probes work by the variations of the electrical resistance between them, with one electrode being the reference electrode and the other being the level control electrode.
The process of conductivity electrodes detects the level of resistance when they are covered in the medium. In some cases, an electrically conductive tank wall can be used in place of one of the electrodes.
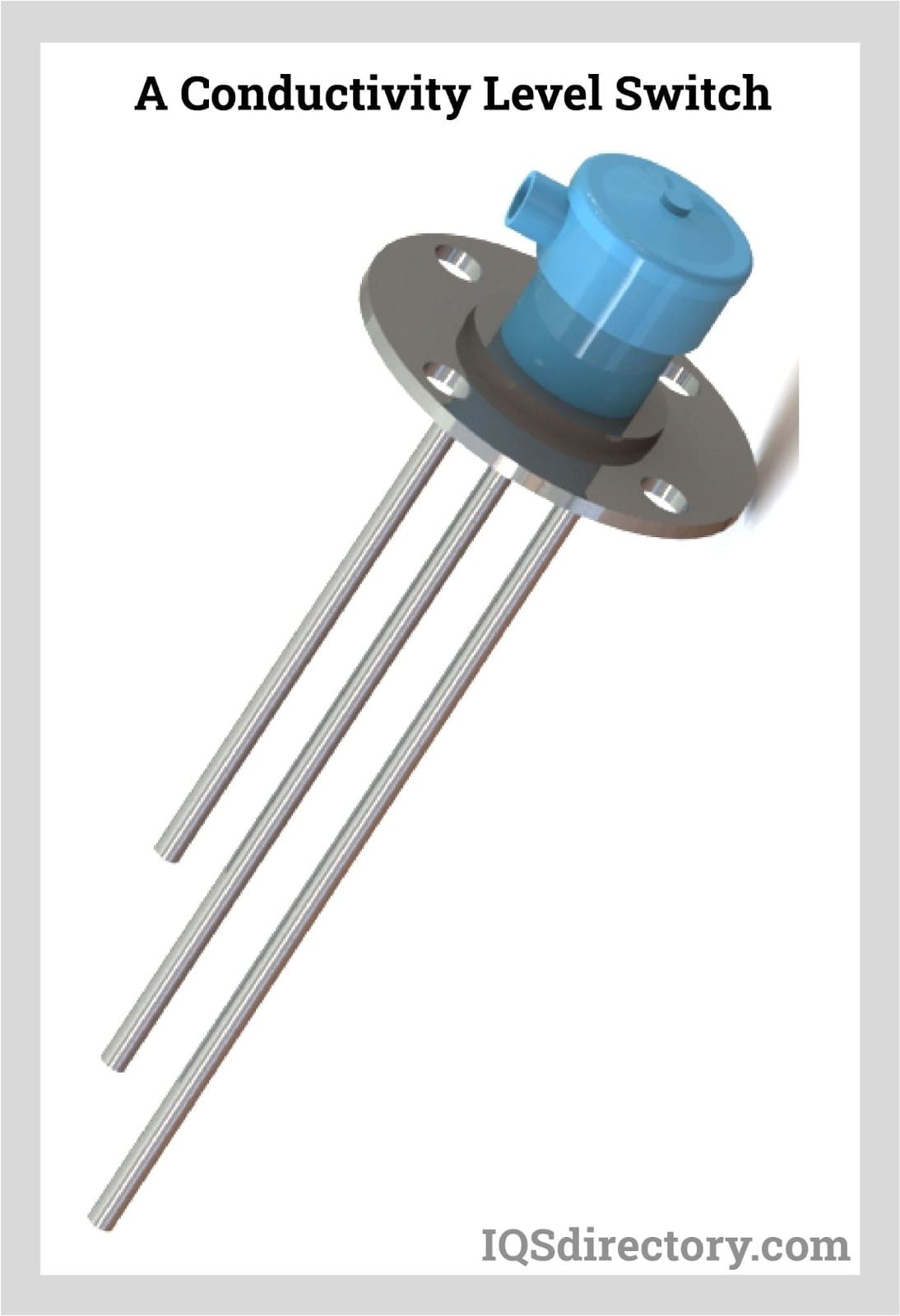
Diaphragm Switch
A diaphragm level switch measures pressure changes caused by the level of the material rising or falling. As the level rises, air pressure gets higher, and the face of the diaphragm falls under the pressure, which activates a micro switch. When the pressure gets lower, the diaphragm returns to its initial position. Diaphragm level switches have an electrical contact output and have wide industrial use.
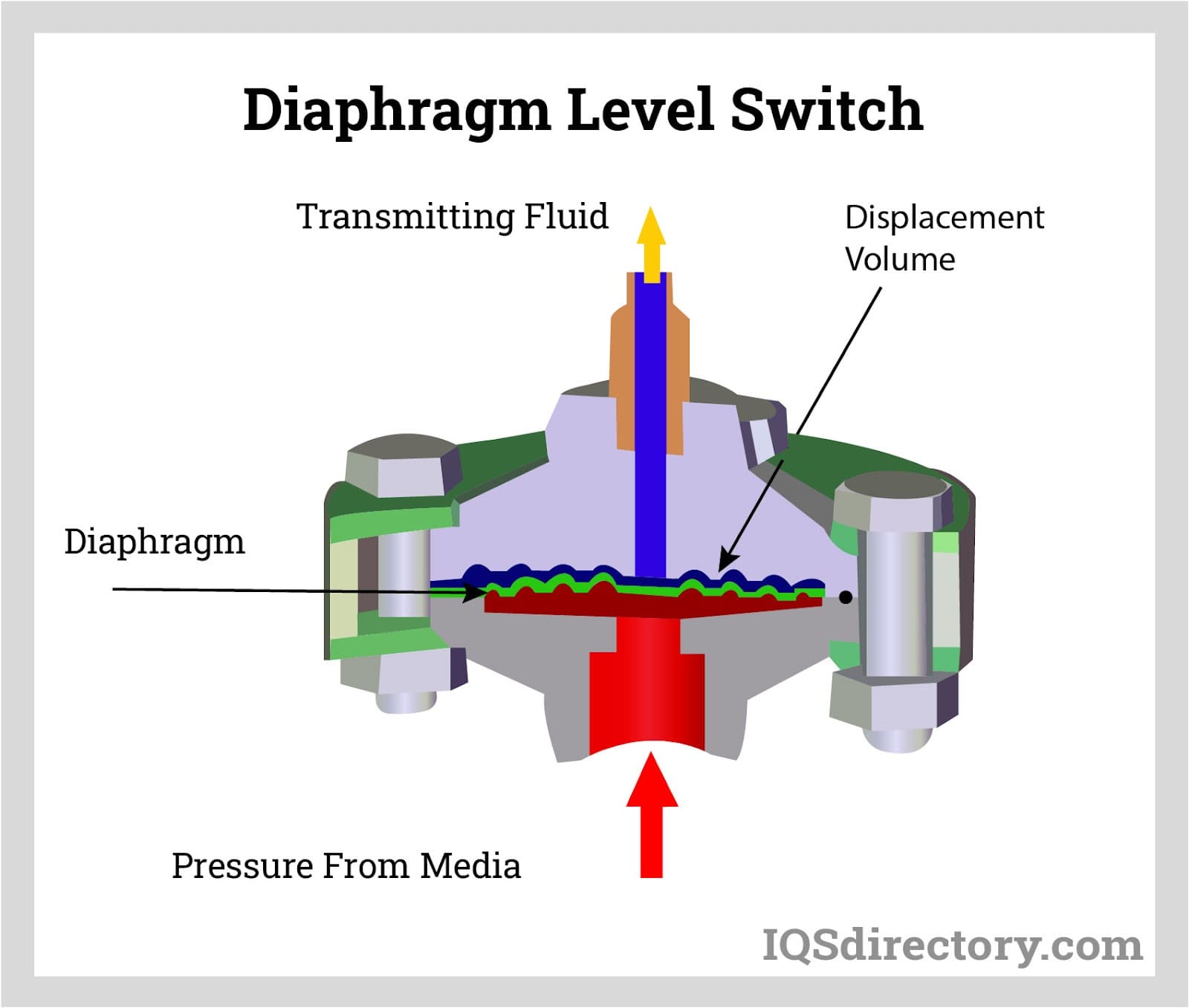
Displacer Level Switch
Displacer level switches are designed to work where there are high temperatures and pressure. They have a weight, which is its displacer, suspended on a spring that is heavier than the media. When the media makes contact with the displacer, buoyancy force is produced that changes the weight of the displacer and causes the spring to retract. As the spring retracts, it sends a magnet upward that actuates the switching element.
In some configurations, three or more displacer level switches may be used to monitor a media at various levels.
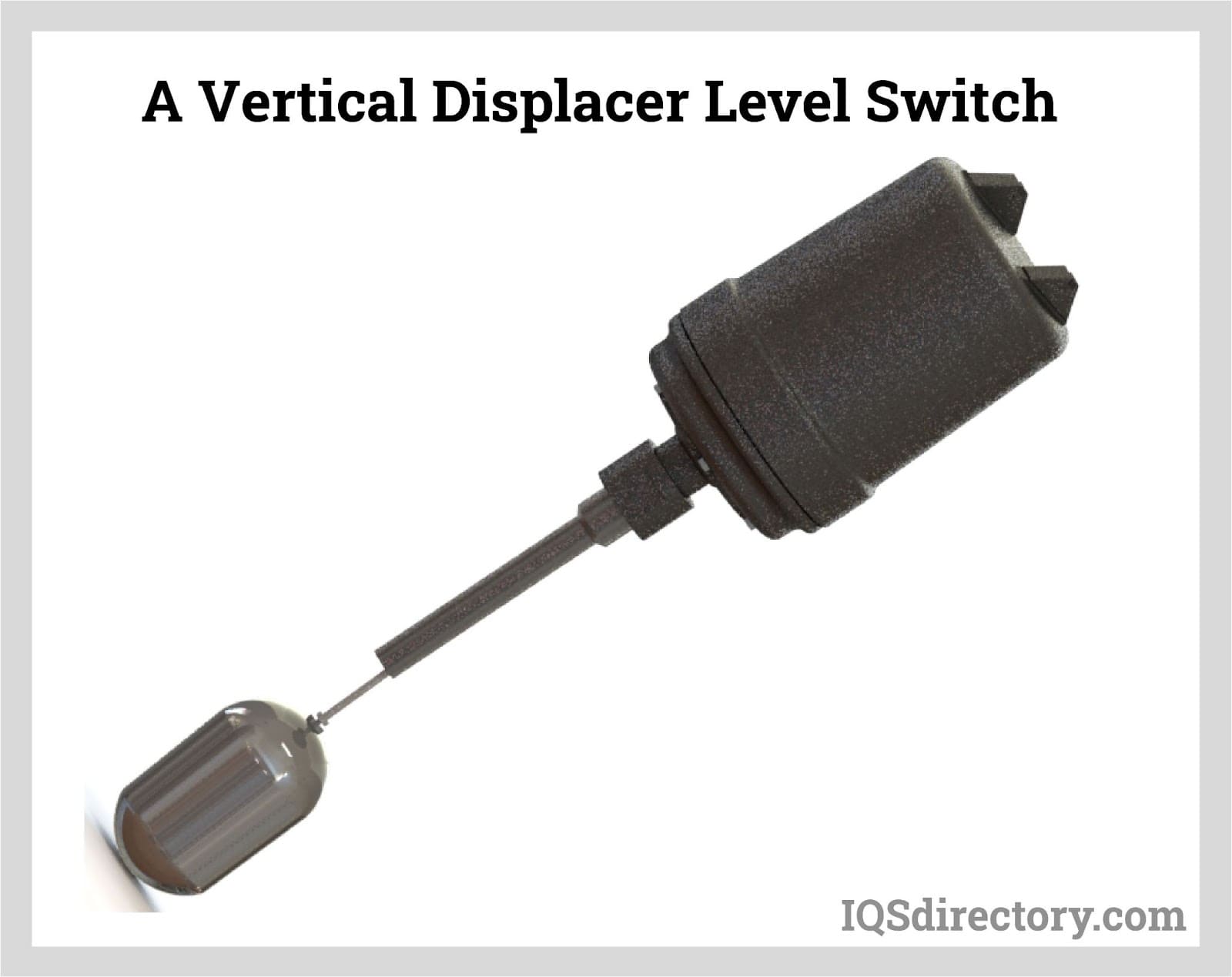
Float Level Switch
A float level switch is a mechanical switch that floats on the surface of the media and moves up or down as the media rises or falls. They are commonly used with pumps, valves, or alarms. Float switches are a cost effective and reliable level switch that can be used with a wide variety of media.
The construction of a float switch includes a hollow body that contains a switch or sensor, which is normally a reed switch with a magnet inside. The switch opens or closes due to gravity and the level of the media. Float switches are preset to trigger when the level is outside its set limits. The switch sends a message to a mechanism to open or close a connected device.
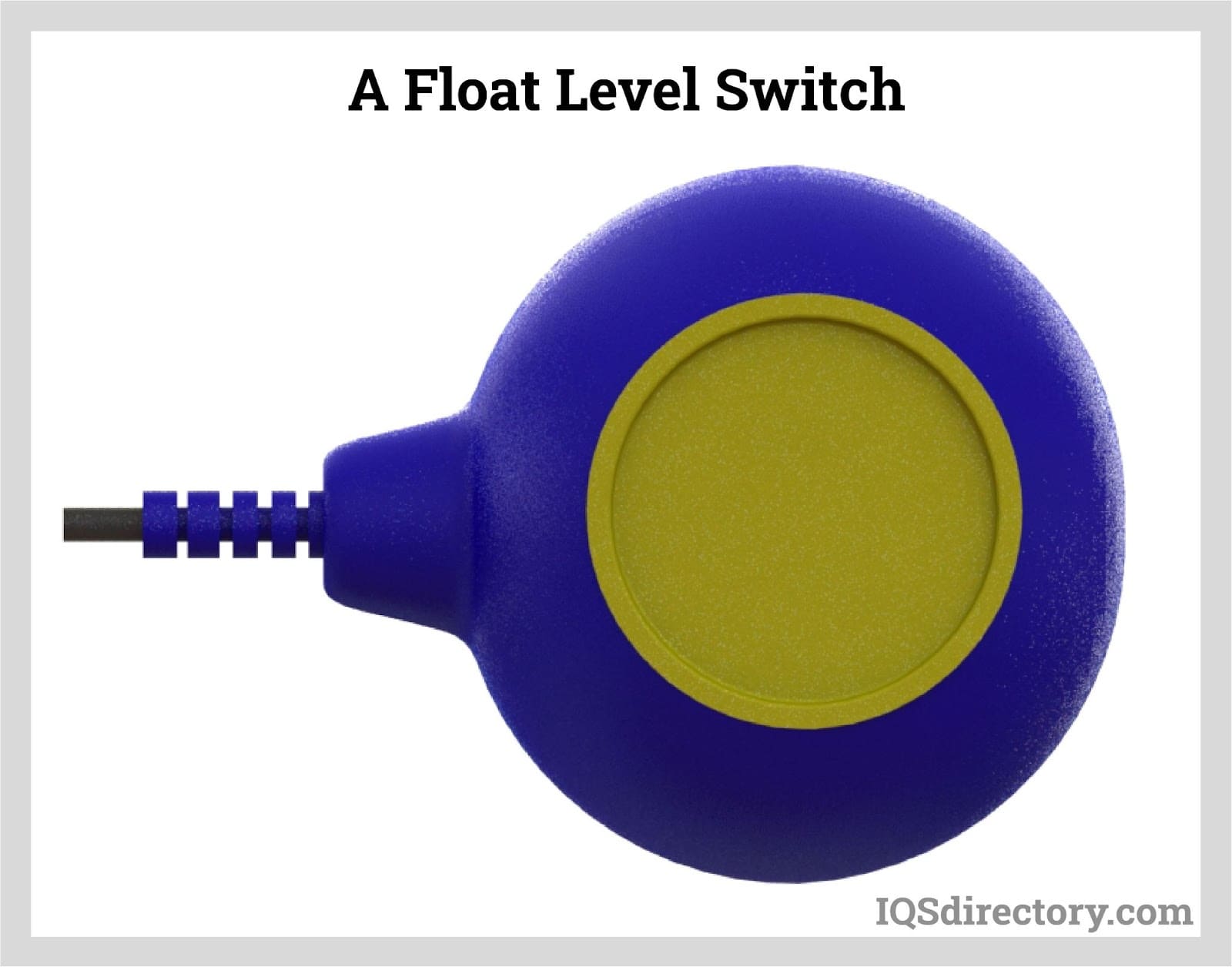
Hydrostatic Level Switches
Hydrostatic level switches are a threshold contact that contains a pressure switch or pressure sensor placed in a solid state NPN or PNP switch. All liquids are influenced by gravity and produce hydrostatic pressure, which is similar to the weight of a solid object. With liquids, it is possible to measure the weight of the liquid in relation to its level. The weight of the liquid at different levels is proportional to a specific level.
Hydrostatic level switches are continuous level measurement switches mounted on the side of a container using a flange, threaded port, or sealed clamp.
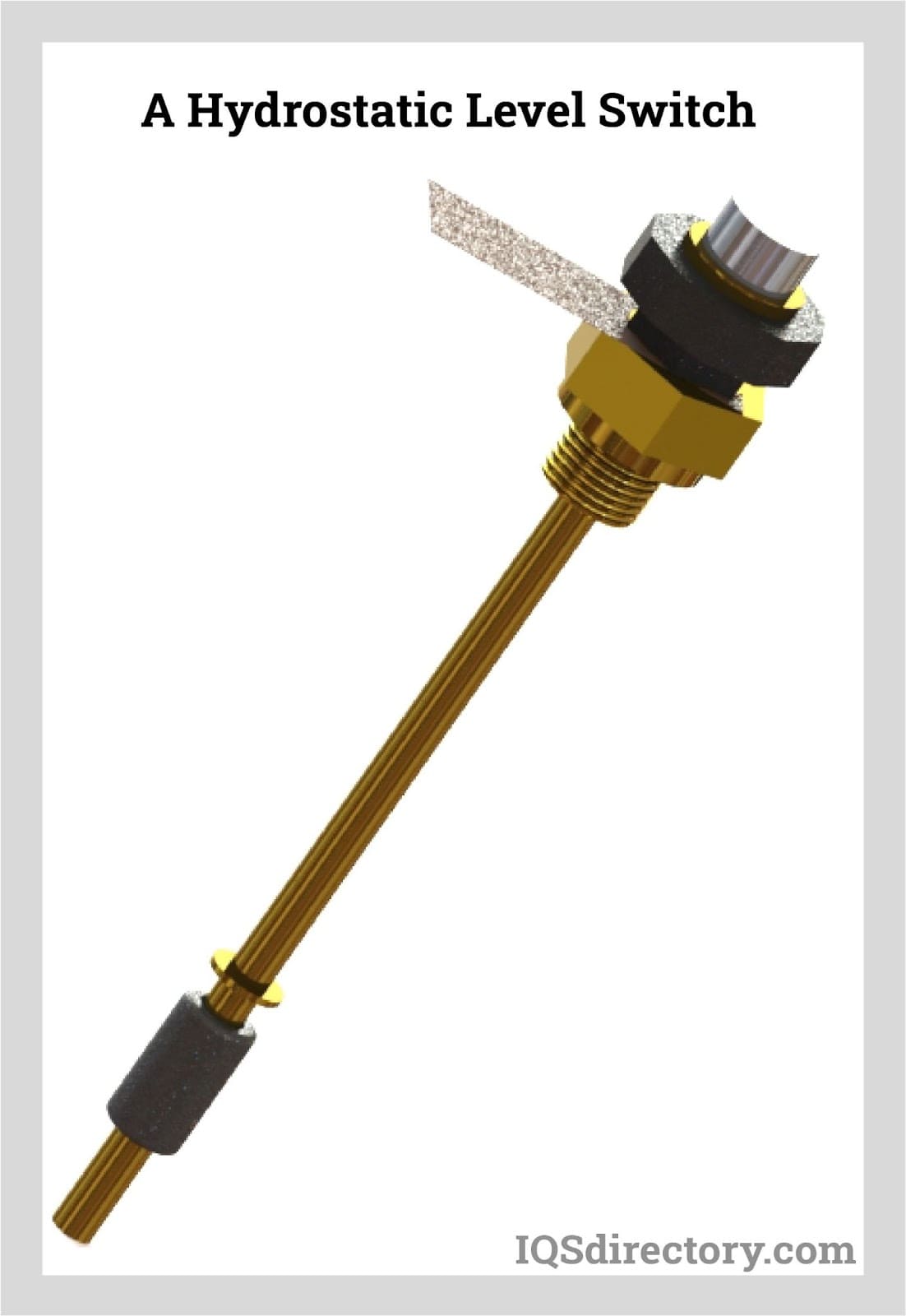
Inductive Level Switches
Inductive level switches are non-contact switches that respond to a targeted material when the material comes within the sensing field. An oscillator resonant circuit uses an open core coil to produce a concentrated high frequency electromagnetic field that comes from the surface of the sensor. If a material enters the target area, eddy currents are produced.
When detection is made, the amplitude of the oscillating unit decreases, and the oscillator is attenuated. The lower amplitude of the oscillating unit sends a signal to the electronic circuit that changes the switching state of the inductive level switch.
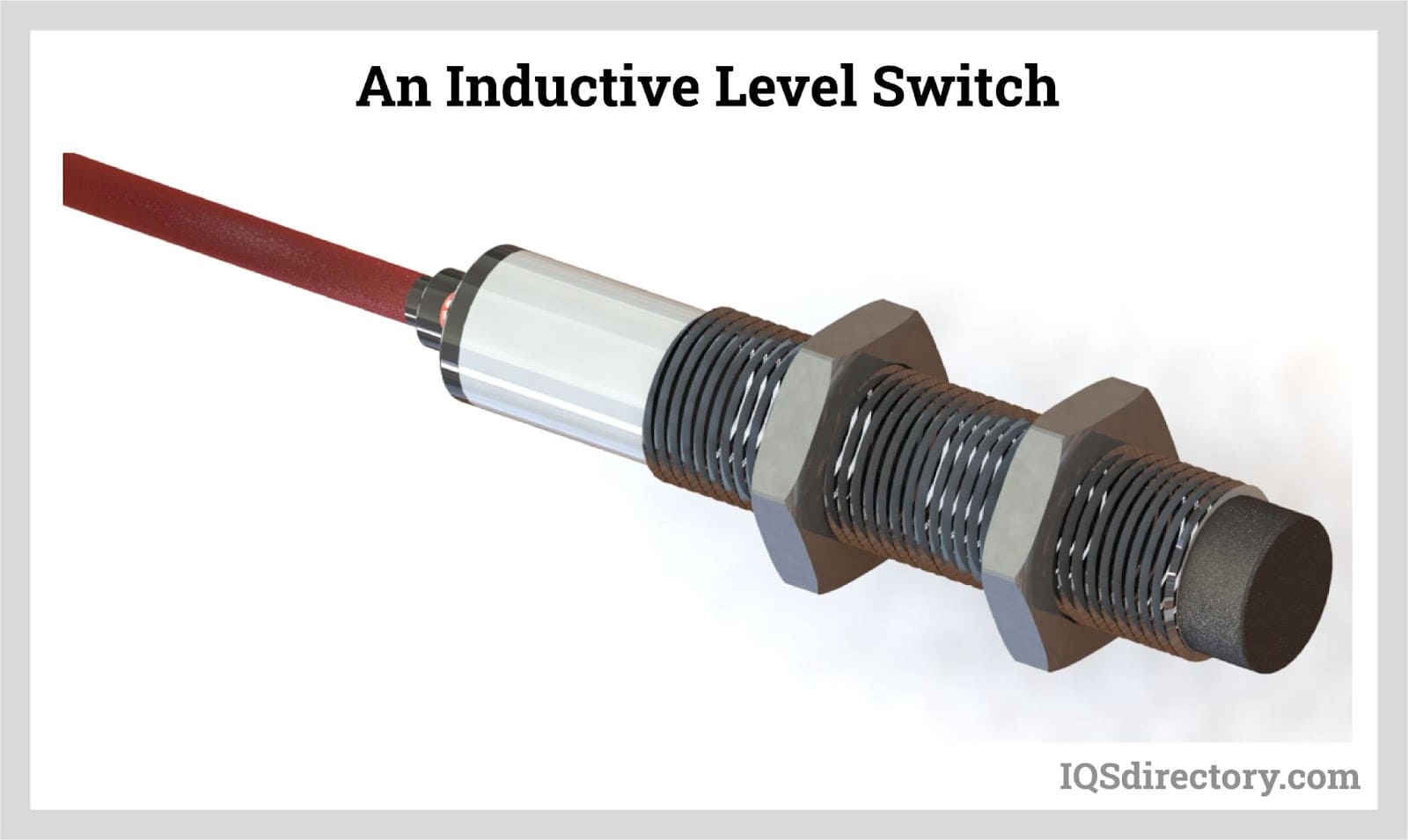
Laser Sensor
A laser sensor is a non-contact level switch that takes level readings using the speed of light. A laser transmitter, at the top of the container, shoots a short pulse of light down to the surface of the process material. The light reflects back to the detector. Like an ultrasonic level switch, a timing circuit measures the ToF to calculate the distance.
The key to lasers is the lack of a beam spread or false echoes and can be directed through a very small space. Laser level switches are very versatile and can measure vapors and foam.
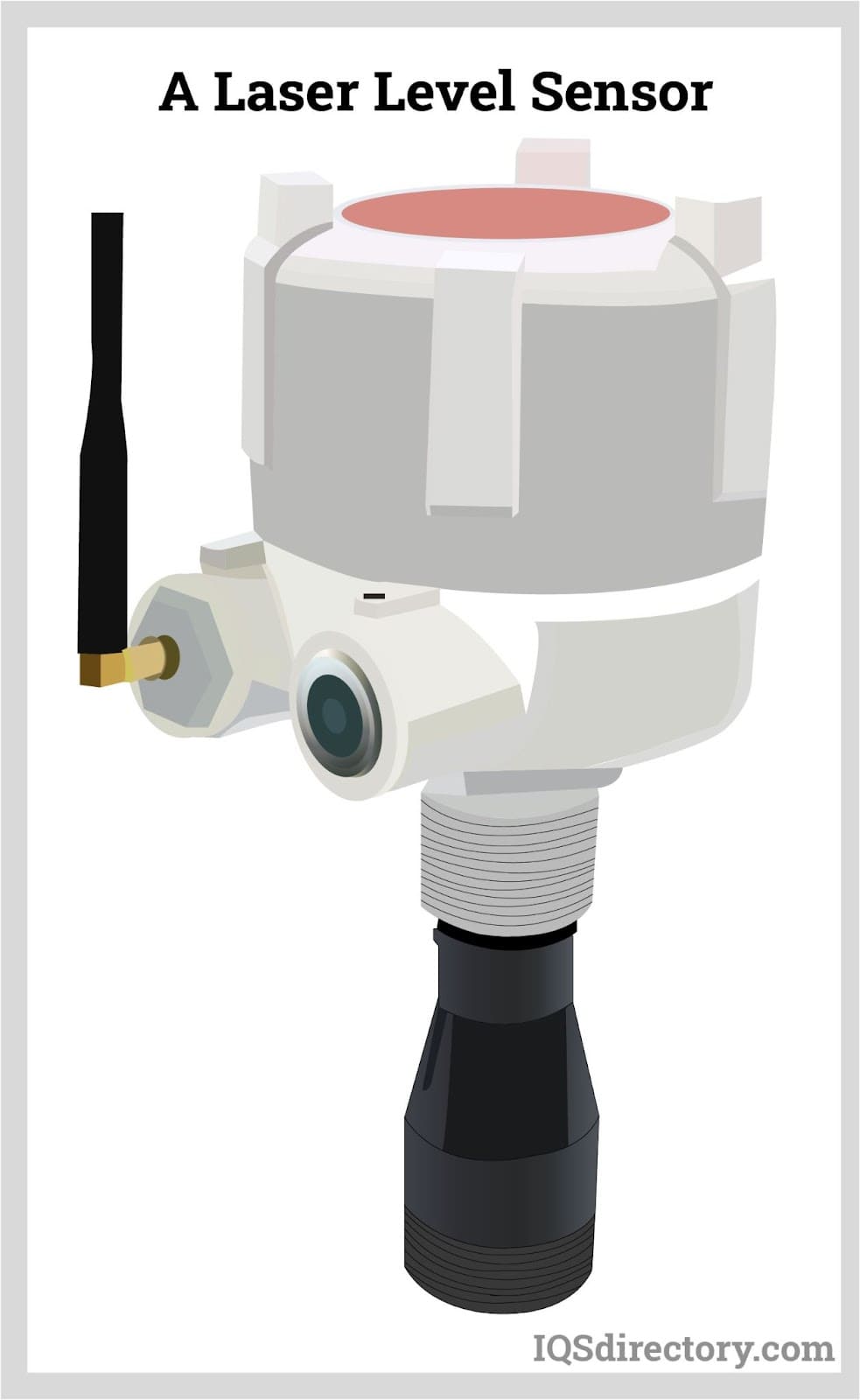
Magnetostrictive Level Switch
A magnetostrictive level switch senses the level of a fluid by detecting the level of magnets in the float and sends the data back to the control system. It uses buoyancy, magnetostriction, and electronics to measure levels. A float that travels up and down due to its buoyancy is mounted on the level transmitter stem. In the float is the magnetic element.
An electrical current pulse is sent the length of the switch through a sensor wire to the location of the float. A timing circuit measures the pulse and its return signal. The signal provides the location of the float and the level of the media.
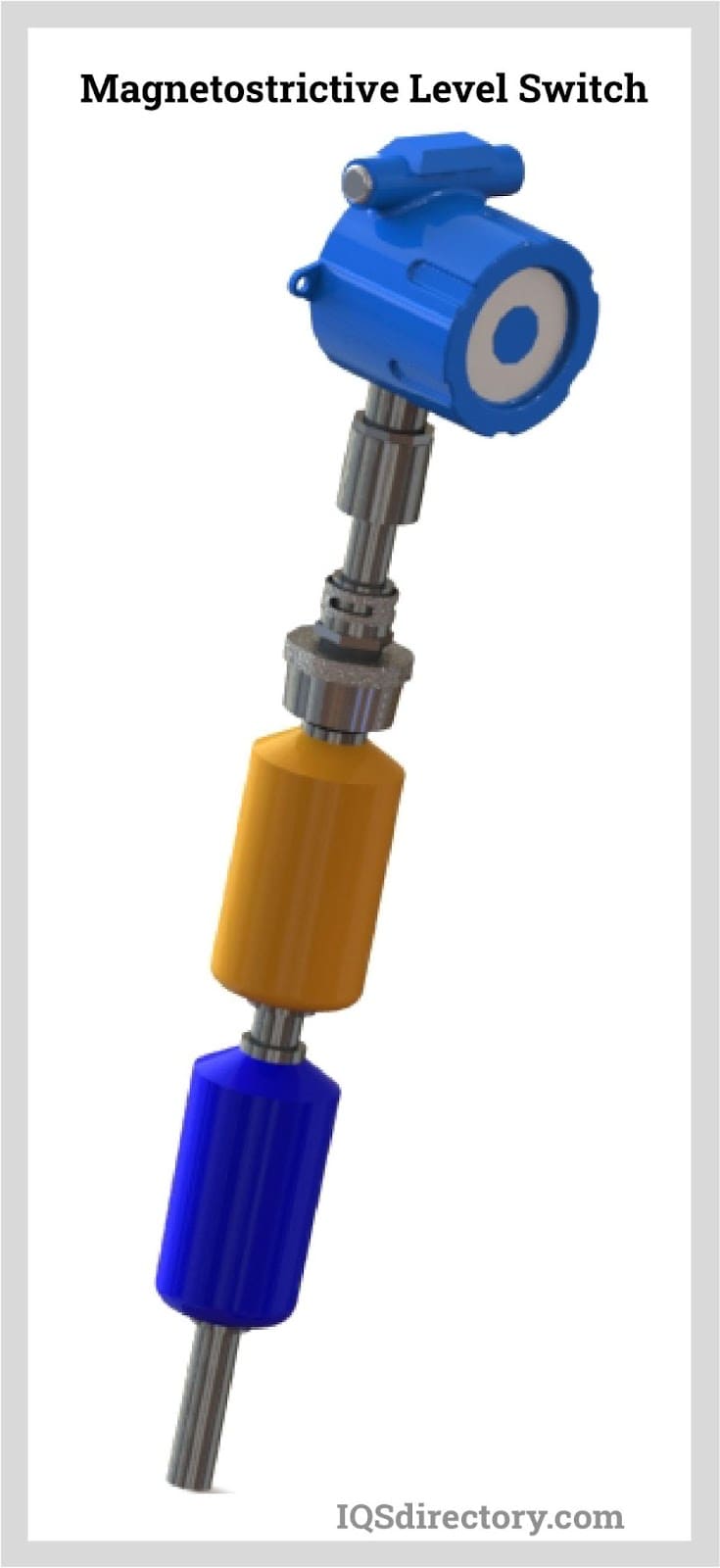
Microwave Level Switches
Microwave level switches are non-contact level switches that use a microwave beam that passes from a sender to a receiver in bursts at 220 times per second. If the bursts are blocked and fail to connect with the receiver by being absorbed or reflected by the material, a relay is activated.
The uses for microwave sensors are in applications where contact with the medium will erode or damage a contact sensor and where there is high temperature, pressure, and aggregate material.
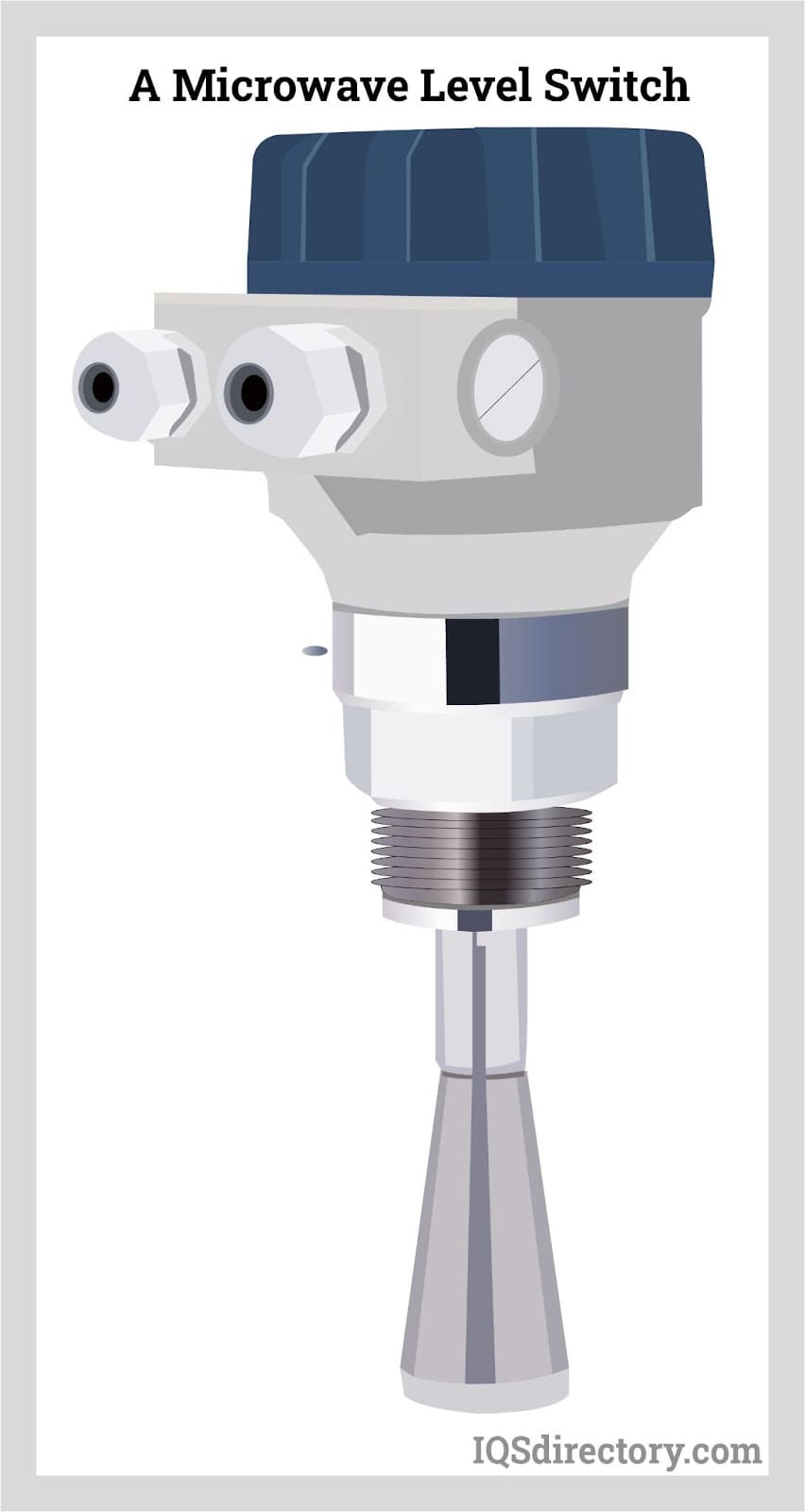
Optical Level Switch
An optical level switch uses the concept of reflection in a prism and is used for high temperature and pressure applications. It can be used as a point level detector and continuous measurement level switch for solids and liquids. A reflected light is sent to the receiver of the sensor and is refracted by the liquid being monitored.
The main components of an optical level sensor are an infrared LED and a light receiver. They sense the decrease or changes in the level using infrared light sent from an infrared diode. Light is sent to a cone shaped prism. When the cone is above the liquid, it is reflected back to the detector. If the cone is below the level of the liquid, the light won't be reflected. When the detector does not receive returned light, it activates an alarm or control.
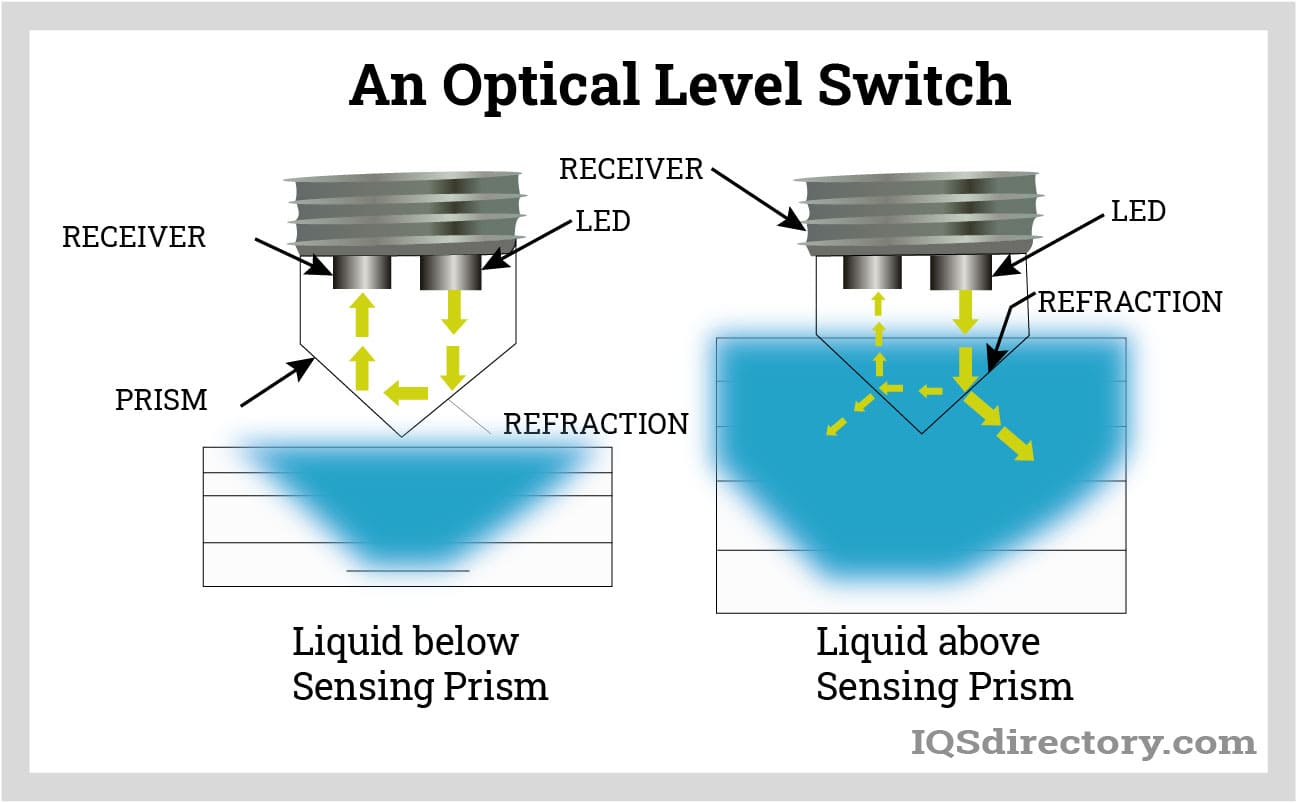
Paddle Level Switch
A paddle level switch has an electric motor that slowly rotates a metal paddle. When the material in the container reaches the level of the paddle, the material will place a load on it. A torque switch, attached to the motor of the switch, activates when a sufficient amount of torsional stress is placed on the paddle.
The design and purpose of paddle level switches are to perform point level detection in dry bulk materials. The paddle of the switch is turned by a one rpm magnet driven motor. As the product builds up in a container, the movement of the paddle is blocked, activating an alarm.
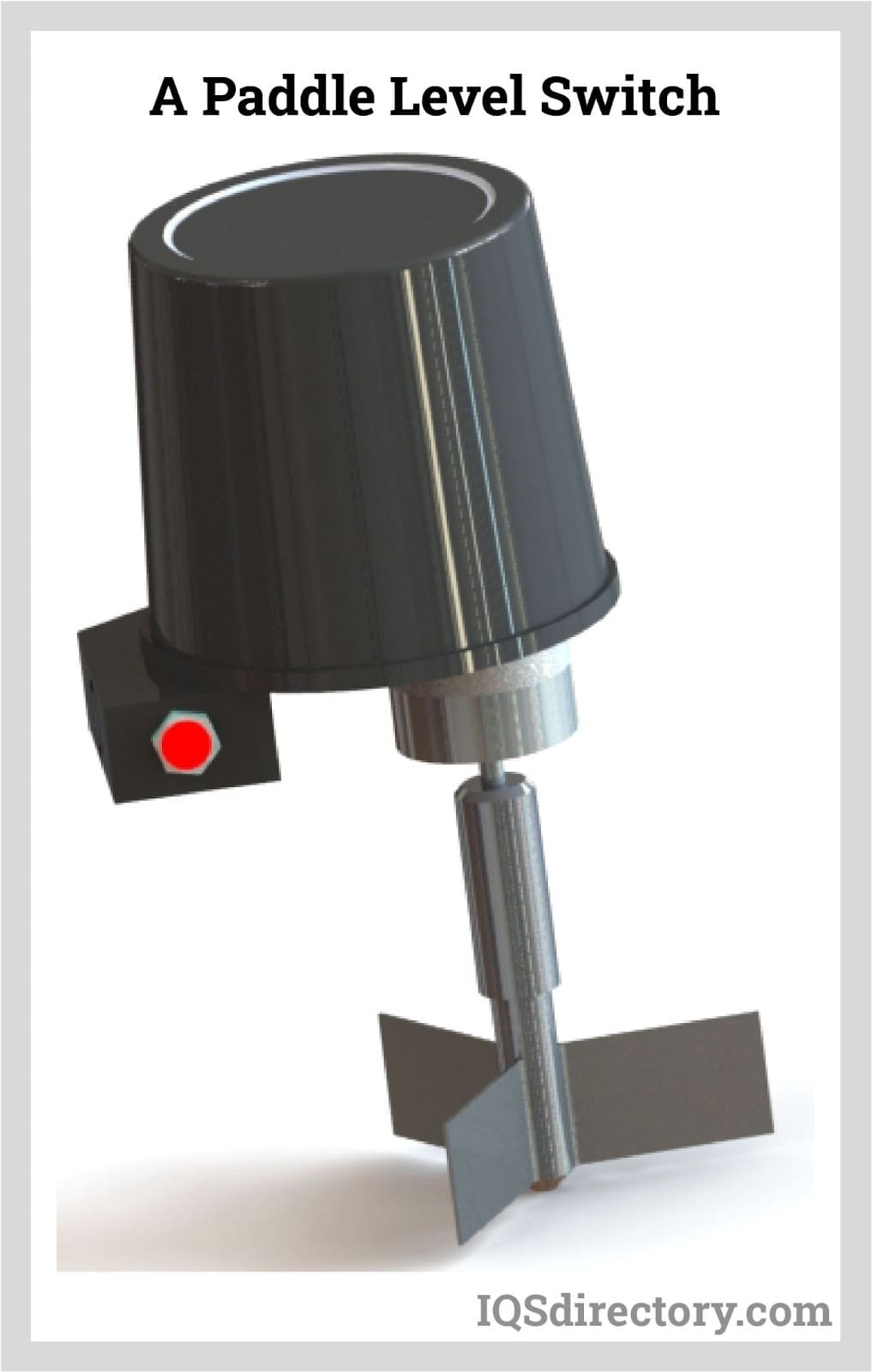
Potentiometric Level Switches
Potentiometric level switches are continuous level switches that are used in metal containers. A low resistance measuring tube is immersed in a conductive liquid, such as an adhesive or paste. A high frequency current is sent through the tube. A voltage reading is taken from the space between the probe and the tank wall, which is sent to an amplifier. The sent reading is proportional to the tank level.
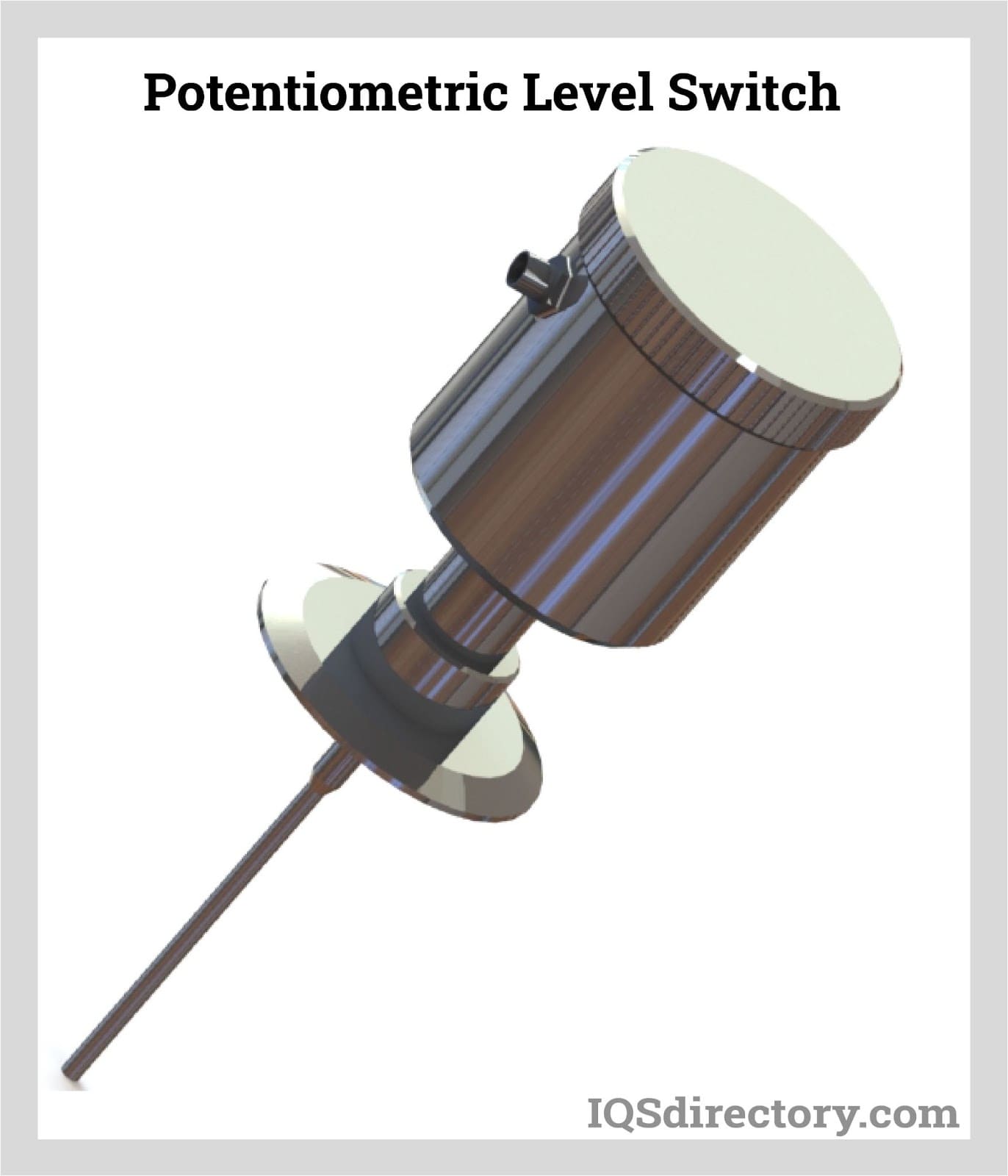
Rod Level Switch
Rod level switches have a stainless steel rod that vibrates or oscillates at a specific frequency and is powered by an electronic circuit. When the media reaches the vibrating rod, the vibrations stop and alert the control system. Rod level switches are a point form of level switches used as high and low level indicators or for plugged chute detection. They are designed and shaped to resist buildup, which would send false alarms.
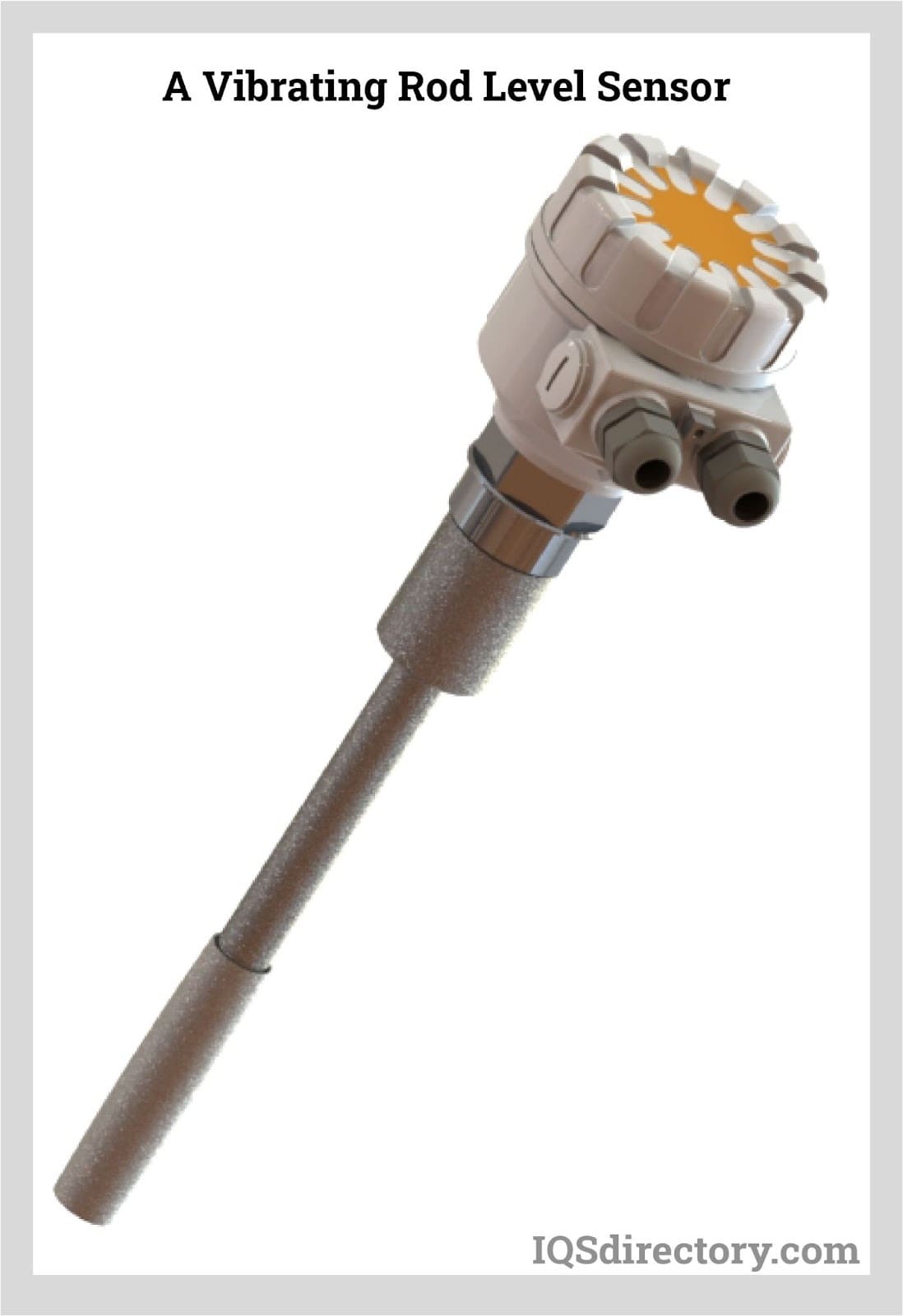
Thermal Level Switches
Thermal level switches sense the difference in the temperature of the vapor space and the liquid or the increase in thermal conductivity as a probe is immersed in a liquid. It consists of a heated thermal resistor or thermistor that is constantly heated. The switch is actuated when there is a drop in the heated temperature of the thermistor.
There are several varieties of thermal level sensors with two resistance temperature detectors (RTDs).
Since heat dispersion is higher in liquids than in a gas or air, the resistance of the thermistor probe changes sharply when it is placed in a liquid. Thermal level switches are accurate up to 1000° C.
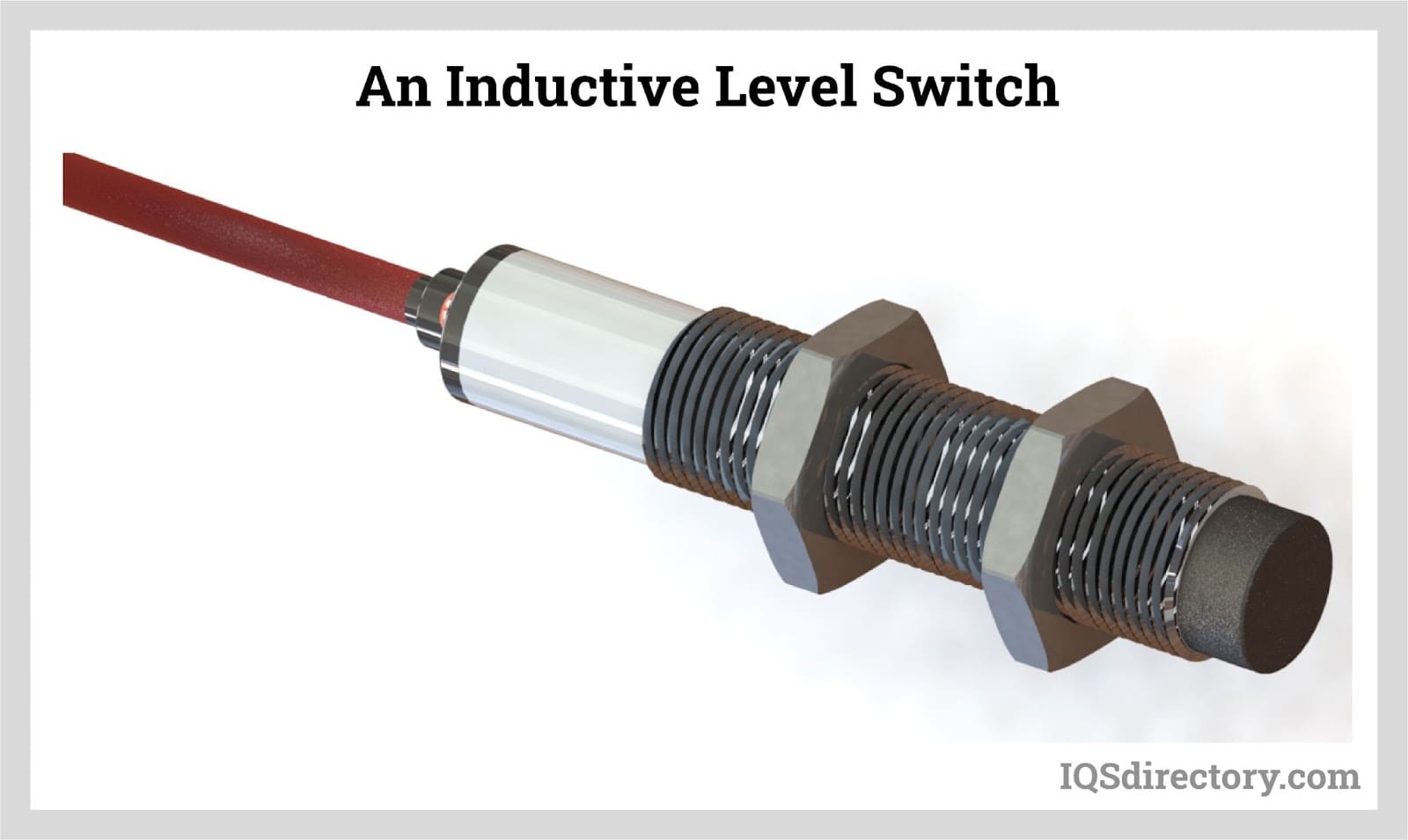
Tilt Level Switches
Tilt level switches are high level indicators that are suspended on a cable above the material. As the media rises and contacts the switch, the switch tilts to the side. Tilt level switches are designed to prevent bin overflow and control levels in open pipes. They are also used for over or under loads for conveyor systems.
The sensor activates when it is tilted at an angle of 17° of a 360° axial arc. The switch includes a threaded bore for attaching actuators, which increases sensing repeatability and protects the switch from contact with the media.
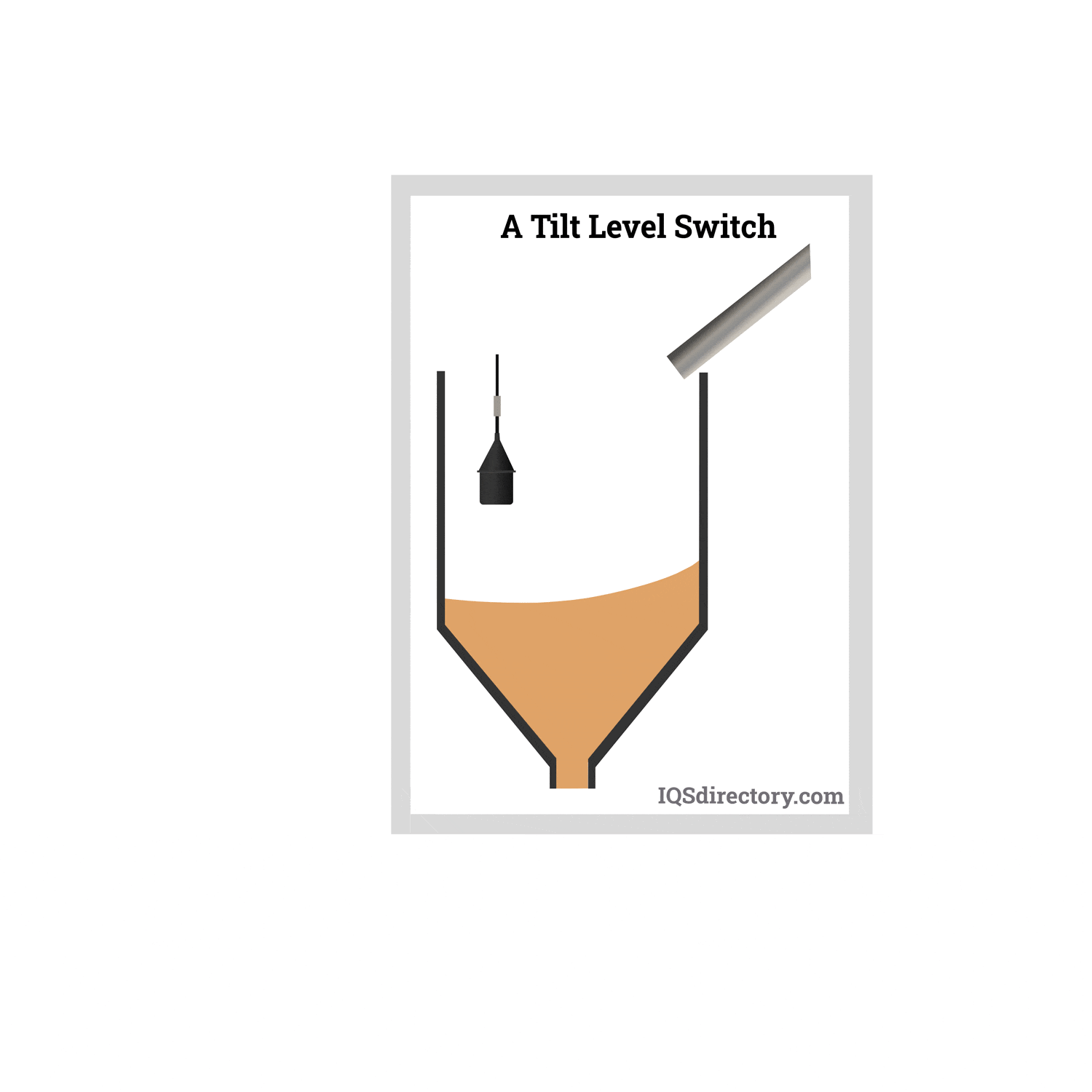
Tuning Fork Level Switch
Tuning fork level switches use frequency changes to alert of level changes in a liquid. The switch has two tuning forks that oscillate in a circuit. The forks are configured to vibrate at the frequency of air. All media has a density greater than air, which causes the tuning forks to vibrate at a lower frequency inside the media.
The forks extend from the switch housing and make contact with the media. When the media makes contact with the forks, the feedback resonant frequency changes indicating a change in the level of the media.
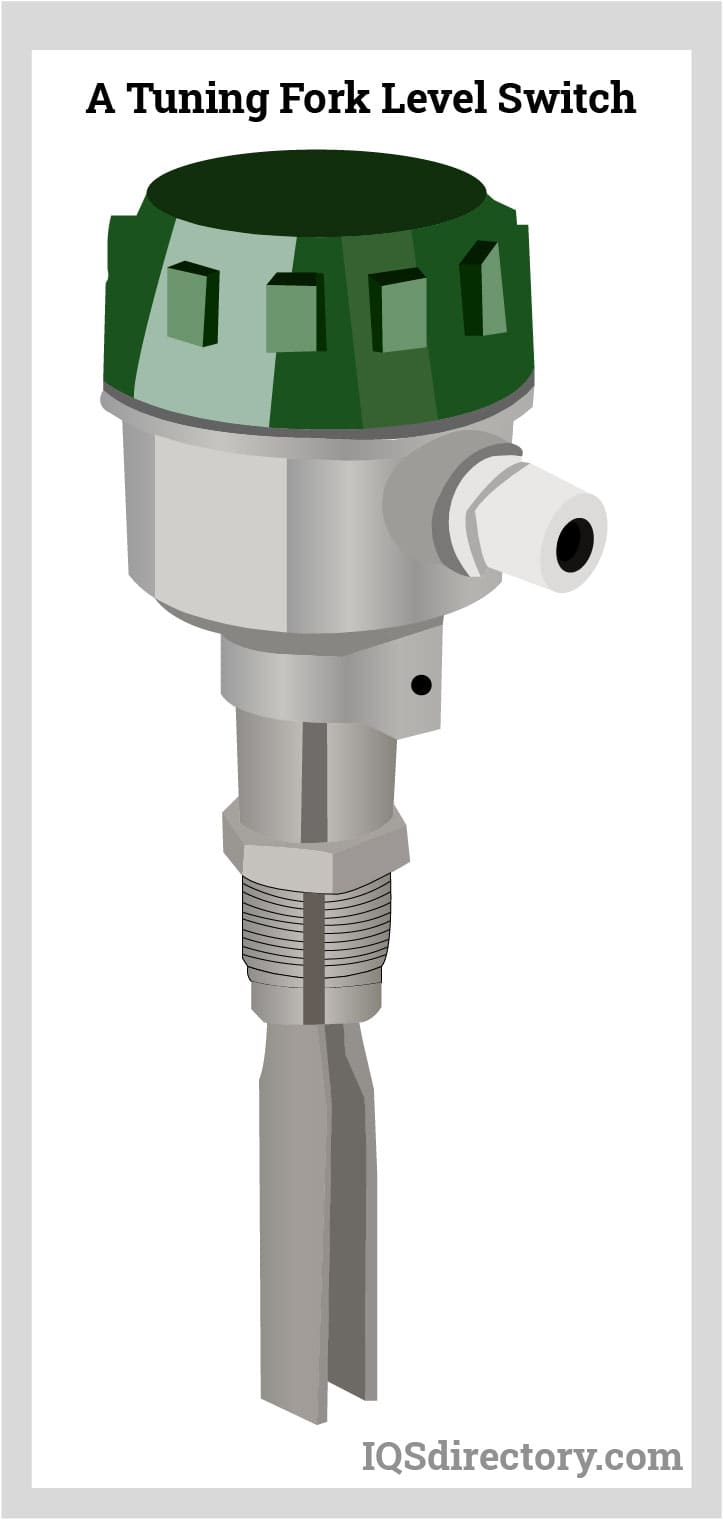
Chapter Three – Level Switch Applications
A level switch is designed to serve a single purpose: to notify or alert controllers when there is the detection of a problem with a product's level or presence. It signals the system when the measured level is outside the programmed parameters. Once notified, the system may activate a pump, open a valve, or take appropriate actions.
In the simplest terms, a level switch is an extra layer of protection and control to ensure efficiency and protect sensitive equipment. Errors in readings can occur at any time regardless of the precision of a system. Level switches help to avoid overfills, waste, and other possible problems.
Applications of Level Switches
Point Level Detection
A point level detection level switch is programmed with a predefined level and activates when that level is reached. Level switches used for point level detection include capacitance, ultrasonic, rotary paddle, and tuning fork or rod vibration switches. In the point level switch system, there are two switches with one to measure the high level and one to measure the low level.
A high level switch allows a container to be filled without overflowing, while a low level switch activates and alerts controllers that the container needs to be refilled.
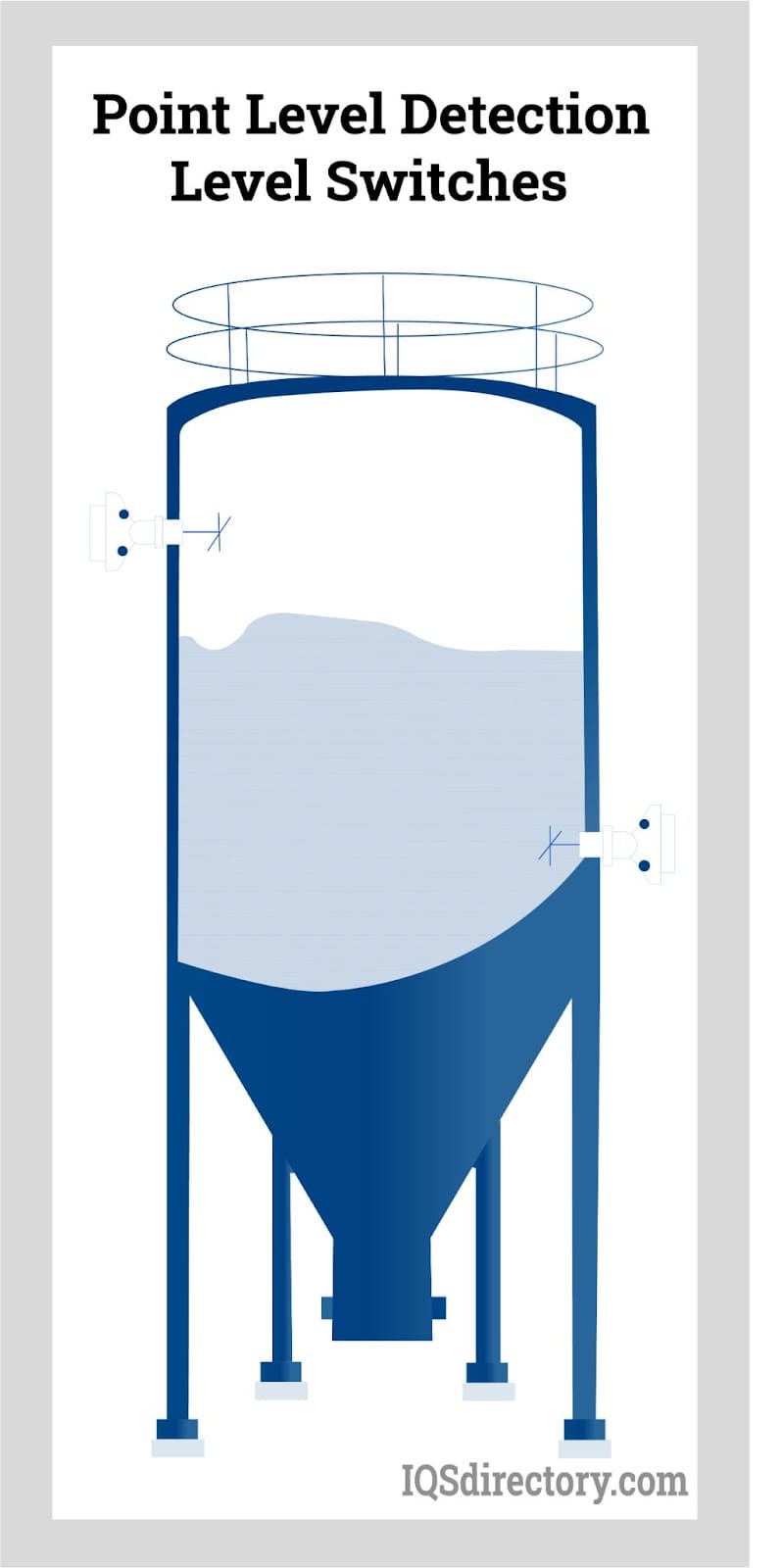
Continuous Level Measurement
Continuous level measurement level switches monitor the levels of media and provide a constant flow of data regarding the media's level. They include microwave, ultrasonic, capacitive, and float switches. Continuous level measurement level switches are more complex than point level detectors since they are designed to monitor the whole system. They are programmed to check a range of levels to produce an analog output of a container's level.
There are two different methods for installing continuous level measurement level switches, which are horizontal and vertical. The main purpose of these switches is to monitor and control materials stored in confined and restricted areas. Continuous level measurement level switches provide constant and continuous feedback regarding the level in a container, which is essential for processes where the level is important, and increased accuracy.
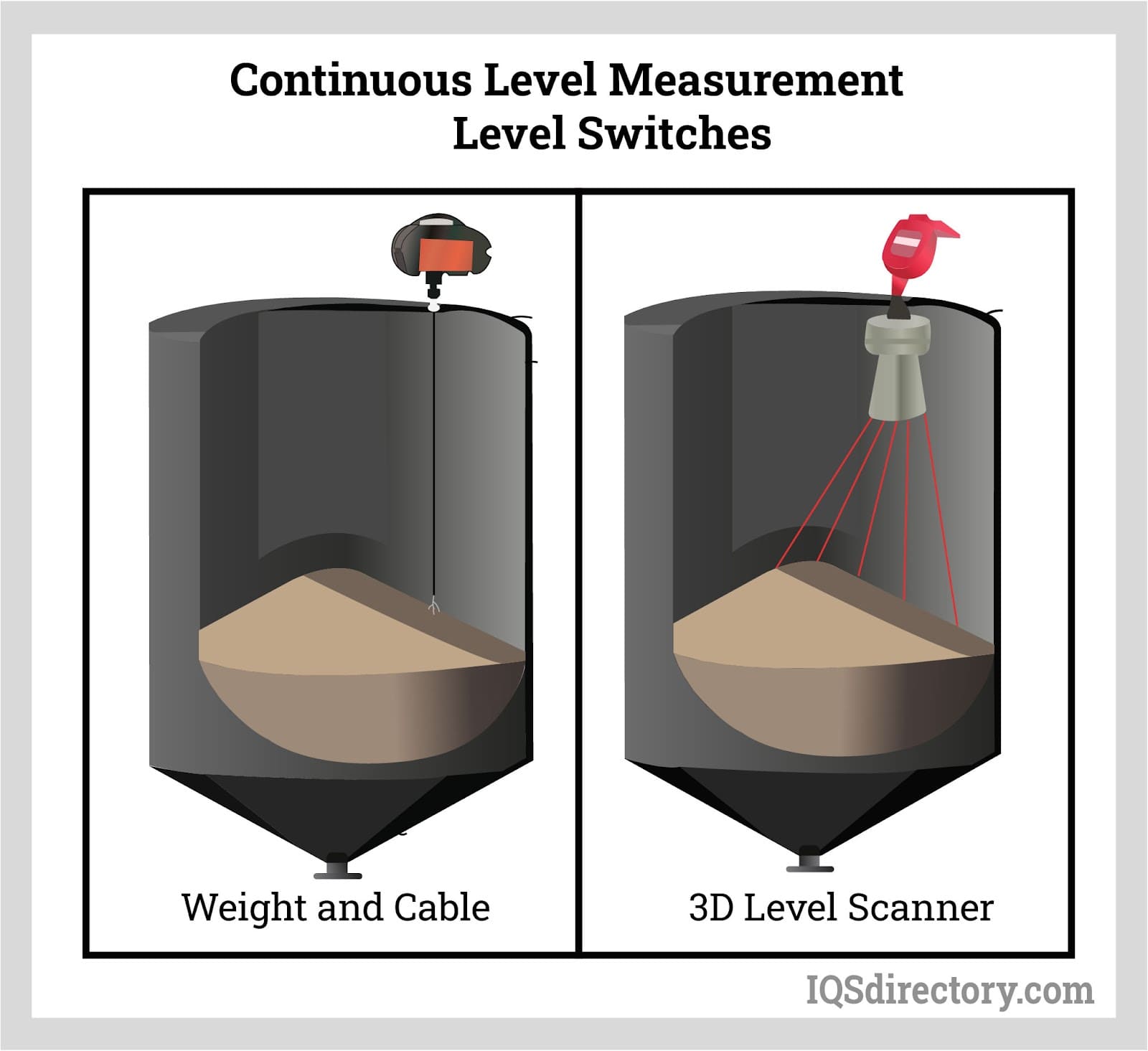
Contact Level Switches
Contact level switches come in contact with the measured product or material and include floats, conductive, and vibrating or tuning fork level switches. They are a very cost effective and straightforward tool for measuring process levels. Unlike non-contact level switches, contact level switches have fewer features and a simplistic design. An important concern for contact level switches is the configuration of the material they will measure, such as corrosive, acidic, or highly reactive. Though contact level switches are less expensive, they have to be chosen carefully to match the medium.
Contact level switches use several mechanical principles. They are capable of monitoring bulk solid materials and liquids or fluids. Contact level switches rely on the buoyancy principle and have floats, displacers, springs, or magnets.
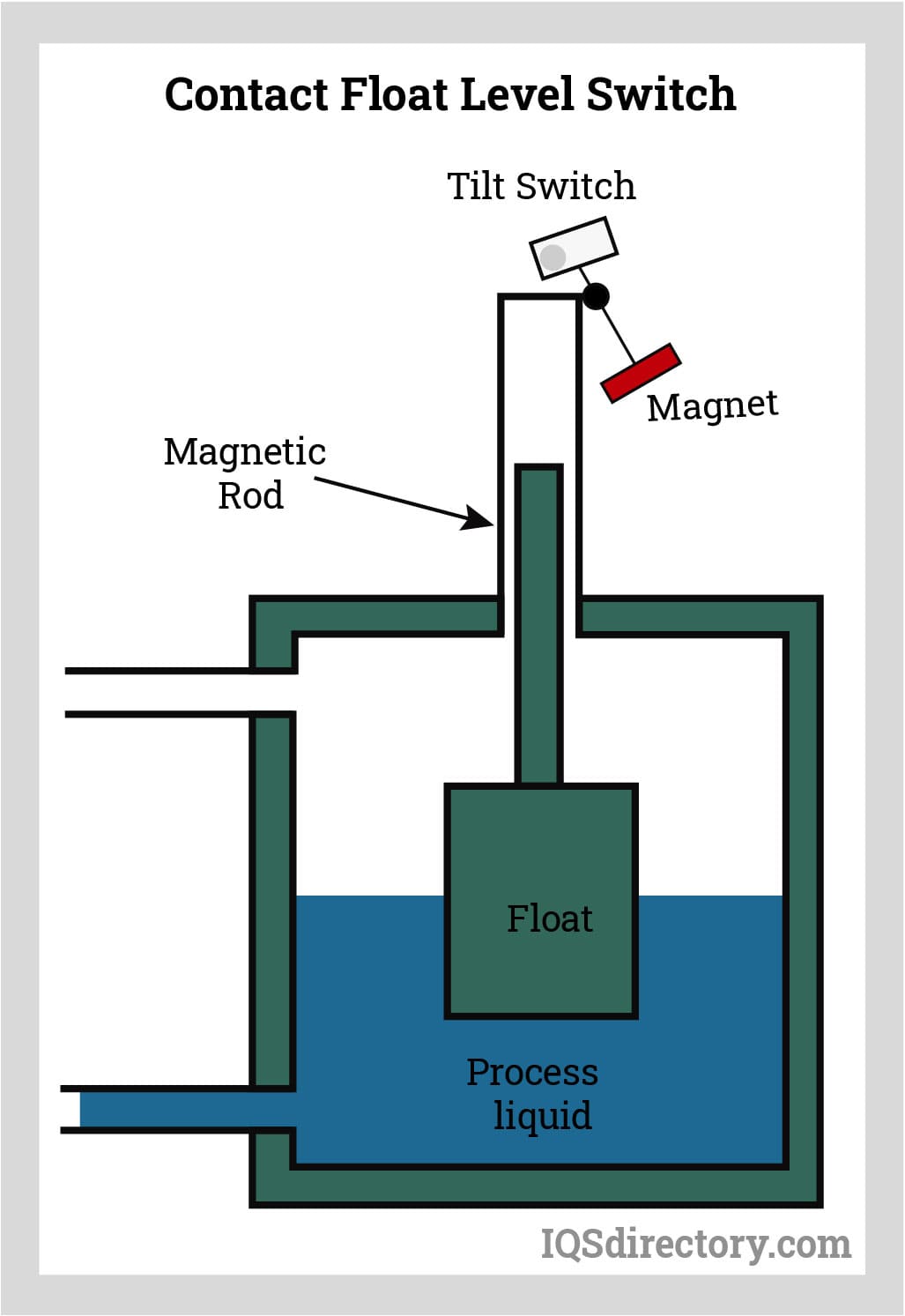
Non-Contact Level Switches
There are certain applications where contact with the medium has to be avoided because the product is corrosive or has properties that would taint the function of the level switch or its readings. Non-contact level switches use the time of flight (ToF) principle to measure the level of a material continuously.
ToF devices measure the time it takes for waves to travel from one point to another and back. They transmit mechanical or electromagnetic waves that bounce back when the waves make contact with a surface. The travel time of the waves can be used to calculate the distance between the receiving device and the contents of a container, which is the level of the container's contents. For non-contact level switches to function properly, the medium being measured must have a very minimum dielectric constant, interfering with the level switches readings.
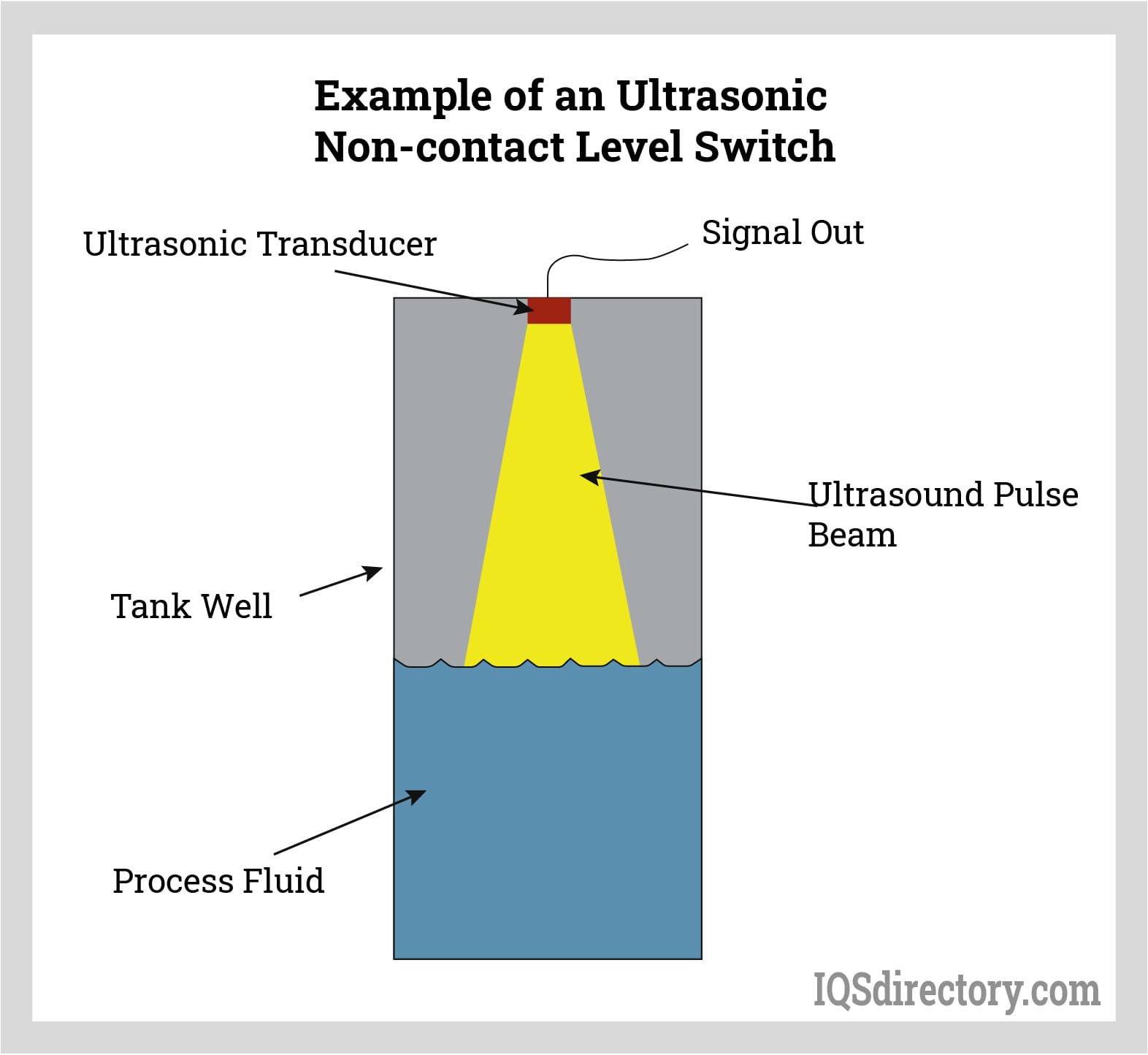
Chapter Four – How a Level Switch Works
Though the function of a level switch is rather simple and fundamental, they are an essential part of a system designed to protect resources and equipment. Any process that relies on bulk materials or liquids has to maintain and control the quantities and volume of the material. Several highly technical computerized forms of software are designed for that function. In many cases, level switches are the main component for supplying data and monitoring materials.
Level switches keep processes rolling and assist in controlling inventories by providing data and measurements. They detect volume errors and send alarms to notify users of any problems.
Components of a Level Switch
Sensor Component
The main component of a level switch is its sensor, which can be point level detection or continuous level measurement. Point level sensor indicators include capacitance, optical, conductivity, vibrating or tuning fork, and float switch. Sensors for continuous level measurement are ultrasonic, microwave, and radar.
Point level sensors are very small, inexpensive, make contact with the product, have no moving parts, and are very accurate. To ensure their accuracy, they are calibrated to the proper level and type of product.
Continuous level measurement sensors have no moving parts, are compact, extremely reliable, do not make contact with the product, are unaffected by the properties or characteristics of the product, and are self-cleaning. Since continuous level measurement sensors are more complex, they are more expensive and can be affected by environmental factors such as static electricity.
Output Signal
The output signals for a level switch can be serial or parallel, depending on the type of level switch and its design. Serial output is a method of communication between a computer and its peripherals, which, in this case, is a level switch. The data is sent sequentially with a starting point and stopping point.
The types of communication of a serial output signal can be asynchronous, where the data has a start and stop to delimit it. With synchronous serial output, additional bits are eliminated, and the limiting of the data depends on timing. Serial data communication can be sent over long distances and has simple wiring.
Parallel communication involves sending each bit of data on a separate wire. All of the data is received by the computer all at once and must arrive at exactly the same time. With parallel data communication, more information can be sent all at once, quickly and reliably. Since all the data is received at one time, it takes longer to be processed.
Interface
There are various displays available for level switches, with some types being more precise and accurate than others. The three most common types that are used for industrial processes are analog, digital, and video. In the majority of cases, computers are used to control and accept the data.
Certain variations of level switches have unit displays where settings can be made on the switch.
- Analog – As with all analog displays, there is a dial, button, or needle used to set the parameters of the switch.
- Digital – Digital displays are the most user friendly and have numerical readings that can be used to set the levels for the level switch. The display is normally lit and has a method for entering or reading data.
- Computer – More and more systems are connecting level switches to computers to receive the output data, whether it is serial or parallel. A computer is capable of arranging the data and providing a video display.
Chapter Five – The Advantages of Level Switches
Level switches are an economical method for monitoring, controlling, and regulating the levels of bulk materials and fluids or liquids. Every manufacturing process necessitates control of raw materials to avoid waste and ensure efficiency. This has become more important in today's competitive markets, where slight inconsistencies and errors can have multiple effects on production and product development.
The minute and small appearance of level switches may cause them to be categorized and defined as inconsequential. In reality, the minor investment in level switches can lead to the effective use of raw materials.
Level Switch Advantages
Preventing Waste
The control of the storage of bulk and liquid materials assists in avoiding waste from spillage and overflows. A properly programmed level switch can activate a valve or pump to control overflow and avoid losses. With continuous level measurement level switches, the correct amount of raw materials is constantly maintained. Point level detector level switches can sound an alarm when a container is too full or the level is too low.
Money Savings
In modern business, every attempt to save money helps in increasing profits. The inventory and raw materials of a company are its greatest assets and have to be protected, monitored, and controlled to avoid losses. Though there have been substantial developments in the computerization of inventory control, every financial officer knows that there will be losses when the official count is taken.
The commonality of inventory loss necessitates constant monitoring of assets. In the case of bulk materials and fluids, such monitoring can be difficult due to the nature of the products. Level switch manufacturers are well aware of the difficulties associated with controlling the loss of bulk materials and have designed a wide selection of level switches capable of providing detailed data regarding the volume and quantities of on hand raw materials.
Automatic Advantages
Unlike floats, yardsticks, and other methods of product level monitoring, level switches are capable of automatically providing accurate data on time to a computer without the need to activate or initiate another device. In cases where the level switch is not connected to a controller, the data can be read from a digital or analog display with little effort.
For many years, the monitoring of silos, storage tanks, vats, and large containers required a routinely scheduled and constant surveillance of products by personnel. In most cases, the readings were inaccurate and not completed. All the footwork and labor required by the old fashion data collection systems has been eliminated by the automatic reporting level switches.
Reliability Advantage
The design and engineering of modern level switches remove any concern for poor performance or inaccurate data. The casings and materials used to produce level switches ensure that they will provide precise accurate readings for a long time. Since level switches have few moving parts, they do not require repairs or maintenance to accumulate data. Minor calibrations and adjustments may be necessary to guarantee the accuracy of a level switch but its failure is highly unlikely.
Switch Installation
Regardless of the type of level switch, whether it is continuous level measurement or point level detection, installation is easy. They can be installed and operating in an hour or two, depending on the type of switch. The ease of installation makes it possible to move and reposition them when there are changes in storage arrangements.
Compact Benefit
Unlike massive data collection methods, level switches are compact and can be handheld. Their compact design makes it possible to fit them into any size container regardless of its shape, dimensions, or location. Their compact configuration makes it possible to position a switch accurately such that it can collect data without obstructions.
Switch Sensitivity
The main reason for investing in level switches is their accurate sensitivity and ability to provide exceptional precision data. As every manager and supervisor knows, it is impossible to make correct decisions without up to date and accurate information. When materials are being sent from a container to production, they must be in the exact quantities that the process requires. It is for these reasons that level switches are an essential part of inventory control and production operations.
Level Switch Versatility
Regardless of the type of material being monitored, there is a level switch to manage and monitor it. This includes viscous slurries, tar, petroleum, grain, flour, and molten metals. The wide range of level switches is capable of meeting the challenge and performing beyond expectations. This aspect of level switches has made them such an essential part of production and processing.
Chapter Six – How to Choose the Right Level Switch
A level switch is a mechanical or electrical instrument for monitoring and checking the contents of bins, silos, storage tanks, and receptacles. They are used to assist in maintaining the proper preprogrammed level of materials such that they do not fall below a specified point or exceed a specified point.
There are several factors to consider when choosing the right level switch for your application. Some considerations are electrical requirements, types of wires, switch placement or positioning, type of material, and how the switch will be mounted.
Choosing a Level Switch
Level Switch Material
Level switches are made from every type of material conceivable. When determining what level switch to buy, it is important that the level switch be compatible with the material it will be monitoring. Manufacturers make level switches from brass, stainless steel, and various forms of plastic. All of these materials can be used with wet materials that are non corrosive.
The chemical impact from the media being measured can impact the performance of a level switch. This consideration is also a factor in deciding if the level switch will be the immersion type, such as a displacer or float level switch.
Electrical Requirements
For a level switch to work properly, its electrical connection must match its power supply. Insufficient power supply or over supply can lead to poor performance of the level switch or non-activation.
Switch Mounting
As simple as this may seem, the mounting of a level switch has a great to do with its performance and capabilities. Fundamentally, level switches can be mounted horizontally or vertically, which are the most basic descriptions of level switch mounting.
Included in the mounting configurations are the size of hole through which the level switch will be mounted, positioning on the container such as the side, top, or bottom, threaded or unthreaded attachment, hanging or wall mounted, and several other factors each of which must be decided in advance of purchasing a level switch.
Measurement of a Switch
This factor is the reason for purchasing a level switch. It must be decided in advance what type of data required and the method of measurement. All level switches are designed to take accurate readings. The types of readings are determined by how the level switch will be used. Most applications require two level switches, with one to measure the empty level and the other to measure overfill.
It is important to determine what the lowest allowable level will be and how close to the top of the container the contents should be allowed to rise. Some of these factors are decided by the size of the container and its volume.
Material Pressure
All materials produce pressure due to their weight. When choosing a level switch, it is important to understand if the materials being monitored will place pressure on the level switch. If that is the case, there are level switches designed from materials capable of withstanding high pressure conditions.
Temperature Withstanding
In the case of temperature, not all level switches are created equal. The base material of a level switch and its type of wiring will determine the level of temperatures that it can endure. Though all level switches can be used for a variety of applications, only ones that are specially designed are capable of withstanding high temperatures of 1000° C or higher.
Switch Output
Level switches can produce different types of output, which can be a relay, analog, or digital. The type of output has to match the controller that will be receiving the data. The selection includes the type of time delay that can differentiate between using parallel or serial output.
Container Size
All level switches can be easily carried by hand and are small and compact devices. Though this is common to all level switches, some types are easier to fit in certain containers than other types. Of the many factors regarding the selection process, this particular one is the most obvious but is often overlooked due to the general size of level switches. The first step in the selection process is to calculate the size of the container and the number of level switches that will be required.
Some producers like progressive readings from level switches as the contents rise. This can be accomplished with continuous level measuring level switches or precisely placed point level detector level switches.
Conclusion
- A level switch is an electrical or mechanical method for measuring the level of a liquid, powder, or granule material.
- Level switches are an essential part of production operations and are used in harsh conditions with extremes in temperature, pressure, and vibrations.
- There is a type of level switch to fit any type of product or application. They are used as a measurement device, a monitoring control, or as a warning alarm, such as when to turn a mechanism on or off.
- A level switch is designed to serve a single purpose, which is to notify or alert controllers when there is the detection of a problem with a product's level or presence. It signals the system when the measured level is outside the programmed parameters.
- Level switches are an economical method for monitoring, controlling, and regulating the levels of bulk materials and fluids or liquids.
Source: https://www.iqsdirectory.com/articles/level-switch.html
0 Response to "A Magnetostrictive Sensor is a Part of a Continuous Level Measuring System Consisting of a N"
Post a Comment